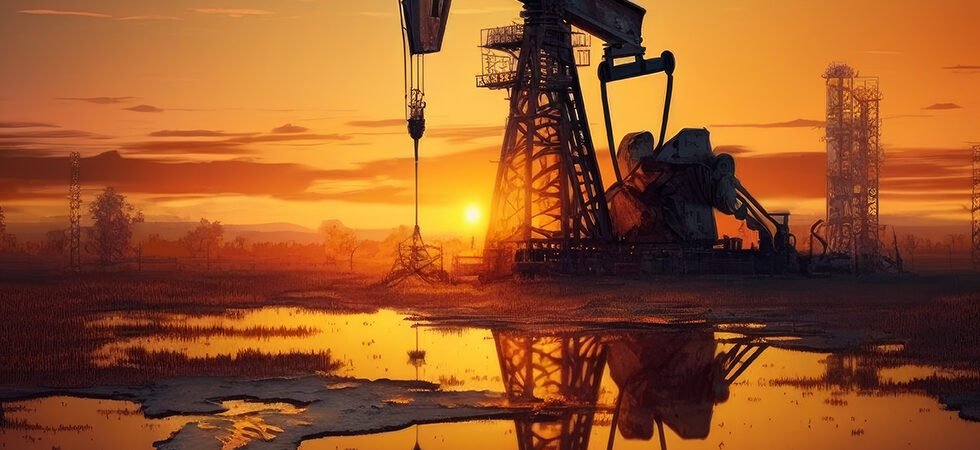
Naphtha Reforming unit with capacity of 150 MTPD
Here’s a breakdown of what that would entail:
Unit Capacity: 150 MTPD refers to the production capacity of the unit. In this case, the unit is designed to process 150 metric tons of feedstock per day. This could involve converting naphtha or other light hydrocarbons into high-value products.
Reforming Process: The catalytic reforming process usually involves:
- Feedstock: A light hydrocarbon (often naphtha) is fed into the unit.
- Catalytic Reactions: A catalyst (typically platinum-based) facilitates chemical reactions that reconfigure the molecular structure of the hydrocarbons.
- End Products: This process results in valuable products like high-octane gasoline, aromatics (such as benzene, toluene, xylene), and hydrogen.
Key Factors to Consider:
- Catalyst Selection: The right catalyst is crucial to ensuring high efficiency and product quality.
- Feedstock Composition: The type of naphtha or other hydrocarbon feedstock influences the reforming process and the products obtained.
- Energy Consumption: Reforming is an energy-intensive process, requiring careful optimization of temperature, pressure, and flow rates.
- Hydrogen Management: Depending on the setup, hydrogen produced in the reforming process can be utilized within the unit itself or exported for use in other processes.
Equipment:
- Reactor Vessels: These are where the catalytic reforming reactions take place.
- Heat Exchangers: To maintain the required temperatures and recover energy.
- Separation Units: To separate different products after the reactions.
Control and Monitoring: Given the complexity of the process, continuous monitoring and control are crucial for maintaining the desired product quality and optimizing the operation of the unit.
Let me know if you’d like more specific details on designing, operating, or optimizing a 150 MTPD reforming unit!
Problems
roblem: Catalyst Deactivation in a 150 MTPD reforming unit reduces process efficiency and product quality due to impurities in feedstock, such as sulfur and carbon.
Solutions
- Regular Regeneration of the catalyst to restore activity.
- Pre-treatment of Feedstock (e.g., hydrotreating) to remove contaminants before entering the reforming unit.
- Optimized Catalyst Selection: Use advanced catalysts resistant to poisoning.
- Monitoring and Control: Implement a robust system to track feedstock quality and adjust operating conditions to maximize catalyst life and process stability.
Results
By implementing catalyst regeneration, feedstock pre-treatment, and optimized catalyst selection, the 150 MTPD reforming unit can maintain high efficiency and product quality. Monitoring and control systems help ensure consistent feedstock quality and optimal operating conditions, extending catalyst life and improving process stability. These measures significantly reduce the impact of catalyst deactivation, ensuring better yield, lower operational costs, and improved overall performance of the unit.